CRANE INDUSTRY
Complete visibility of your crane fleet and operator compliance
One platform for a high level view
QuipCheck has a ready-made solution tailored for the crane industry. Our fully customisable application caters for all types of cranes including mobile, pick-and-carry, crawler and tower cranes.
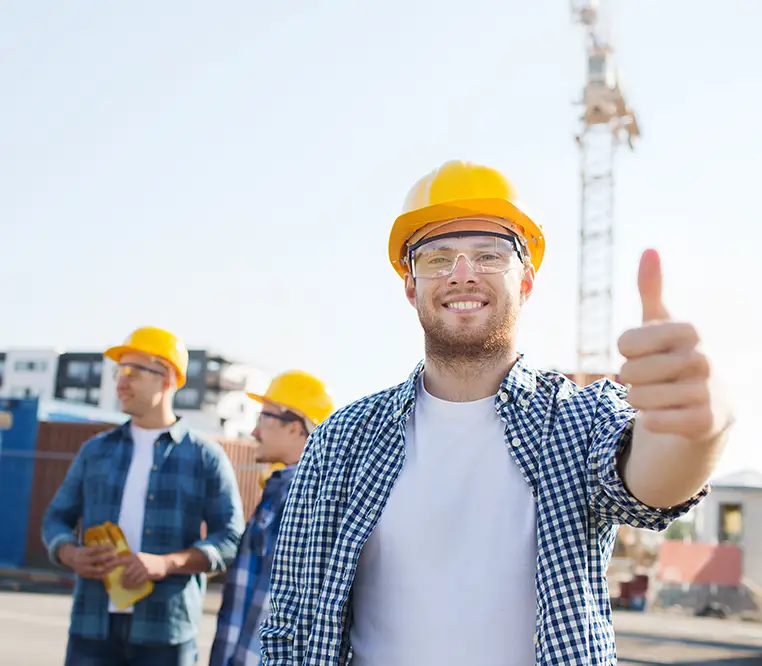
Streamline your crane fleet management with QuipCheck™
QuipCheck is being used by crane operators and service technicians in the crane industry to undertake pre-start checks, record service and maintenance work, track service intervals, manage rigging gear and assist with H&S compliance.
Enhanced Safety and Compliance
Digital records of pre-start checks, machinery maintenance, and worker safety data ensure compliance with industry standards. Real-time access to information empowers workers to identify potential hazards promptly, reducing accidents and improving overall site safety.
Increased Efficiency and Productivity
Paperless systems streamline workflows, eliminating time-consuming tasks like manual data entry and searching for physical documents. This frees up valuable time for crews to focus on core tasks, boosting productivity and project completion rates.
Improved Data Accuracy and Accessibility
Digital records provide accurate, up-to-date information on machinery, personnel, and site conditions. Centralised data storage enables easy access for all authorised personnel, facilitating better decision-making, reporting, and analysis.
For checks that get done by everyone.
Our fully customisable application caters for all types of cranes including mobile, pick-and-carry, crawler and tower cranes.
Paperless checks
Pre-checks that get done, submitted and measured – without the paper - and tailored to a type of crane
See past and due service inspections
Track everything from service intervals to histories and inspection certificates for every crane
Manage tasks on cranes and rigging gear
Stay on top of reported issues and tasks so you know what's required with live task updates
Processes that keep your operators safe
Guides to lead operators through processes for health and safety compliance and lift planning
Get QuipCheck up and running for your crane fleet
We'll set you up with best-practice systems for your business
Step 1:
Share your business needs
Tell us about your crane business, its size, and specific challenges you face in managing your plant and operators.
Step 2:
We create your solution
Our team will configure QuipCheck to perfectly match your business operations and requirements.
Step 3:
Experience the difference
Start using QuipCheck and witness the positive impact on your efficiency, safety, and overall operations.
Scott McIntosh
McIntosh Cranes, New Zealand
Try QuipCheck with your crane fleet, today
Contact us for a free personalised demo.